Резкое увеличение объемов строительства, если его удастся достичь с помощью госдотаций, может только стабилизировать цены, а не сделать их доступными. А для достижения поставленной цели необходимо в разы снизить стоимость стройматериалов и стоимость самого строительства. Потому что доступное жилье – это, в первую очередь, дешевые материалы и дешевые технологии. Все прочие вопросы, которые требуют, главным образом, не капвложений, а политической воли, могут и должны быть решены законодателями и местной властью.
Сегодня российские ученые предлагают свои решения, ориентированные на существующий в стране уровень строительной индустрии и качество исходных материалов. Они, как правило, являются более приемлемыми для реализации, чем заимствованные за границей. Одна из таких разработок - стеновой материал «термоблок».
Термоблок (патент РФ RU N 2030527) - изделие размерами 390x190x188 мм, включающее оболочку из песчаного бетона и заполнение из минерализованной цементом технической пены объемной массой 150 кг/м3 .
Оболочки изготавливаются на вибропрессующем оборудовании, предназначенном для изготовления щелевых блоков. На вибропрессах одновременно изготавливаются 10-12 оболочек. Они на следующем технологическом посту заполняются минерализованной пеной и после пакетирования направляются в камеру тепловлажностной обработки. Несущие функции в термоблоке выполняет оболочка, теплозащитные - заполнение из минерализованной цементом технической пены. Ее использование в качестве заполнения позволяет исключить применение в изделии иных базовых материалов, кроме цемента и песка. Изготовление оболочек термоблоков вибропрессованием позволяет калибровать размеры изделий с миллиметровой точностью и производить укладку их в стену на слой цементного клея толщиной до 3 мм, что не только снижает расход кладочного материала, но и значительно повышает теплотехническую однородность стены.
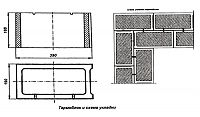
Вибропрессование предоставляет уникальные возможности отделки блоков. За счет изменения формы матрицы можно изготавливать блоки с рельефным, криволинейным и ломаным очертанием передней грани. Введение пигментов в цементно-песчаную смесь позволяет получать цветные блоки. Возможно включенное в технологический процесс окрашивание наружной грани блоков. «Колотая» и «каннелюрная» фактура лицевой грани блока, практически неотличимая от фактуры натурального камня, достигается при изготовлении спаренных блоков и последующим их раскалыванием. Причем оборудование для раскалывания также может быть включено в технологический цикл.
В условиях, когда несущие и теплозащитные функции в изделии разделены, прочностные и деформативные характеристики не являются определяющими для качества термоблока. Более того, даже величина предельной относительной деформации усадки – одна из наиболее значимых характеристик для пенобетона, не является существенной в связи с малым объемом минерализованной пены в отдельном изделии. Наличие цемента в ее составе обеспечивает надежное ее сцепление с бетоном оболочки. В результате исследований был получен высокопоризованный тонкодисперсный пенобетон плотностью 150 кг/м3 с замкнутой однородной ячеистой структурой.
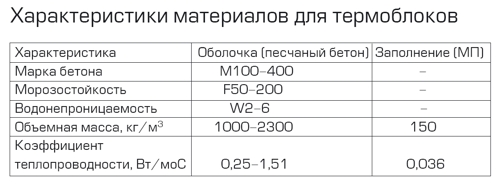
Испытаниями установлены коэффициенты теплопроводности пенобетона «150» в сухом состоянии и при равновесной влажности материала равной 4,7 %, = 0,028 и = 0,036 Вт/моС. Причем в зависимости от требуемой несущей способности и региона строительства оболочка термоблоков должна иметь различную прочность и плотность.
Возможность получения изделий, характеристики которых полностью соответствуют требованиям норм, изделий, выполненных из наиболее дешевых материалов и по технологии, исключающей ручные операции, делают термоблоки наиболее дешевым стеновым материалом России.
Решение основной задачи – получение дешевого качественного стенового материала позволяет строительство мини-заводов, мини-ДСК – предприятий, где из песчаного бетона выпускается вся номенклатура изделий «на дом», включая элементы благоустройства территорий и малые архитектурные формы.
Оборудование включает линию непрерывного формования погонажных предварительно напряженных конструкций (панели перекрытий, балки перекрытий, перемычки, ступени, сваи), линию вибропрессования мелкоштучных изделий (фундаментные блоки, фундаментные плиты, термоблоки, блоки внутренних стен и перегородок, блоки заполнения перекрытий) и два участка – для изготовления цементно-песчаной черепицы и элементов благоустройства. В номенклатуру включены изделия, позволяющие бескрановый монтаж малоэтажных зданий.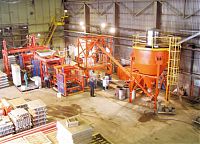
Стоит отметить, что все изделия изготавливаются из песчаного бетона. На мини-заводе не предполагается строительство арматурного цеха: погонажные конструкции армированы только высокопрочной проволокой ВрII без косвенной арматуры и петель. Проволока доставляется на завод в бухтах и не требует дополнительной обработки.
Производительность завода – 20 тыс.м2 в год или 45 тыс.м3 бетонных и железобетонных изделий для строительства 145 одноэтажных домов площадью 95 м2 и 57 двухэтажных домов площадью 122 м2. Основное производство (в том числе камеры ТВО, склад заполнителей, бытовые помещения, лаборатория) размещается в цехе 36х120 м. Для склада готовой продукции не предусматривается строительство отдельного здания. Применяя данную технологию, стоимость квадратного метра в малоэтажном доме площадью 100-120 м2 с наружной отделкой (без земли, коммуникаций, обременений и внутренней отделки) не превысит 8 тысяч рублей.
На данный момент отсутствует объективный анализ существующих технологий и трендов в мировом стройкомплексе. Но при создании предприятий, выпускающих оборудование для производства комплекта изделий «на дом» по технологиям безопалубочного формования, дали бы толчок развитию машиностроения и смежных областей, а также позволили бы координировать стратегию развития сотен разнообразных субъектов в строительстве.
Сегодня российские ученые предлагают свои решения, ориентированные на существующий в стране уровень строительной индустрии и качество исходных материалов. Они, как правило, являются более приемлемыми для реализации, чем заимствованные за границей. Одна из таких разработок - стеновой материал «термоблок».

Оболочки изготавливаются на вибропрессующем оборудовании, предназначенном для изготовления щелевых блоков. На вибропрессах одновременно изготавливаются 10-12 оболочек. Они на следующем технологическом посту заполняются минерализованной пеной и после пакетирования направляются в камеру тепловлажностной обработки. Несущие функции в термоблоке выполняет оболочка, теплозащитные - заполнение из минерализованной цементом технической пены. Ее использование в качестве заполнения позволяет исключить применение в изделии иных базовых материалов, кроме цемента и песка. Изготовление оболочек термоблоков вибропрессованием позволяет калибровать размеры изделий с миллиметровой точностью и производить укладку их в стену на слой цементного клея толщиной до 3 мм, что не только снижает расход кладочного материала, но и значительно повышает теплотехническую однородность стены.
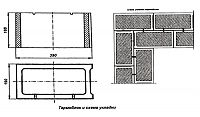
Вибропрессование предоставляет уникальные возможности отделки блоков. За счет изменения формы матрицы можно изготавливать блоки с рельефным, криволинейным и ломаным очертанием передней грани. Введение пигментов в цементно-песчаную смесь позволяет получать цветные блоки. Возможно включенное в технологический процесс окрашивание наружной грани блоков. «Колотая» и «каннелюрная» фактура лицевой грани блока, практически неотличимая от фактуры натурального камня, достигается при изготовлении спаренных блоков и последующим их раскалыванием. Причем оборудование для раскалывания также может быть включено в технологический цикл.
В условиях, когда несущие и теплозащитные функции в изделии разделены, прочностные и деформативные характеристики не являются определяющими для качества термоблока. Более того, даже величина предельной относительной деформации усадки – одна из наиболее значимых характеристик для пенобетона, не является существенной в связи с малым объемом минерализованной пены в отдельном изделии. Наличие цемента в ее составе обеспечивает надежное ее сцепление с бетоном оболочки. В результате исследований был получен высокопоризованный тонкодисперсный пенобетон плотностью 150 кг/м3 с замкнутой однородной ячеистой структурой.
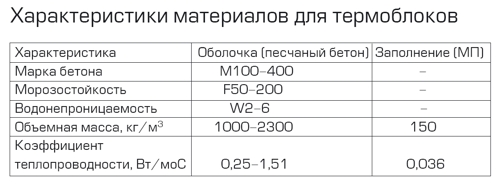
Испытаниями установлены коэффициенты теплопроводности пенобетона «150» в сухом состоянии и при равновесной влажности материала равной 4,7 %, = 0,028 и = 0,036 Вт/моС. Причем в зависимости от требуемой несущей способности и региона строительства оболочка термоблоков должна иметь различную прочность и плотность.
Возможность получения изделий, характеристики которых полностью соответствуют требованиям норм, изделий, выполненных из наиболее дешевых материалов и по технологии, исключающей ручные операции, делают термоблоки наиболее дешевым стеновым материалом России.
Решение основной задачи – получение дешевого качественного стенового материала позволяет строительство мини-заводов, мини-ДСК – предприятий, где из песчаного бетона выпускается вся номенклатура изделий «на дом», включая элементы благоустройства территорий и малые архитектурные формы.
Оборудование включает линию непрерывного формования погонажных предварительно напряженных конструкций (панели перекрытий, балки перекрытий, перемычки, ступени, сваи), линию вибропрессования мелкоштучных изделий (фундаментные блоки, фундаментные плиты, термоблоки, блоки внутренних стен и перегородок, блоки заполнения перекрытий) и два участка – для изготовления цементно-песчаной черепицы и элементов благоустройства. В номенклатуру включены изделия, позволяющие бескрановый монтаж малоэтажных зданий.
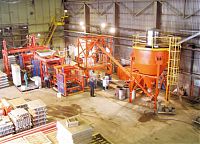
Стоит отметить, что все изделия изготавливаются из песчаного бетона. На мини-заводе не предполагается строительство арматурного цеха: погонажные конструкции армированы только высокопрочной проволокой ВрII без косвенной арматуры и петель. Проволока доставляется на завод в бухтах и не требует дополнительной обработки.
Производительность завода – 20 тыс.м2 в год или 45 тыс.м3 бетонных и железобетонных изделий для строительства 145 одноэтажных домов площадью 95 м2 и 57 двухэтажных домов площадью 122 м2. Основное производство (в том числе камеры ТВО, склад заполнителей, бытовые помещения, лаборатория) размещается в цехе 36х120 м. Для склада готовой продукции не предусматривается строительство отдельного здания. Применяя данную технологию, стоимость квадратного метра в малоэтажном доме площадью 100-120 м2 с наружной отделкой (без земли, коммуникаций, обременений и внутренней отделки) не превысит 8 тысяч рублей.
На данный момент отсутствует объективный анализ существующих технологий и трендов в мировом стройкомплексе. Но при создании предприятий, выпускающих оборудование для производства комплекта изделий «на дом» по технологиям безопалубочного формования, дали бы толчок развитию машиностроения и смежных областей, а также позволили бы координировать стратегию развития сотен разнообразных субъектов в строительстве.
Состав пускового комплекса
• Формовочный цех
Линия КРМ-1025 для производства изделий вибропрессованием производительностью 28 тыс.м3 изделий в год (двухсменная работа, 70% загрузка);
- Линия «Техноспан» для производства железобетонных предварительно напряженных конструкций, производительностью 17 тыс.м3 в год (односменная работа, 70 % загрузка);
- Участок на базе станка ВПЧ-2 для производства черепицы производительностью 25 тыс.м2 в год;
- Участок на базе станка ВИП-6 для производства элементов благоустройства территории производительностью (по тротуарным плитам) 30 тыс.м2 в год;
• Бетоносмесительный узел: два смесителя по 20м3 жесткого бетона в час;
• Склад заполнителей.
По всем вопросам обращайтесь к Константину Иосифовичу Львовичу по телефону 8 903 790 5796.